
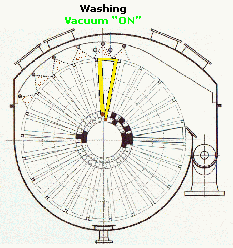
The following are Disk Filter capacities, on average: The capacity of a filter depends largely on the nature of the material to be filtered, particularly the amount of fine material and slimes and the percent solids. All filtrate drains by gravity down the grooves in the disc segment to the drainage pipe and out the valve, before discharge of the filter cake. The exclusive gravity drainage feature of this filter gives the driest possible product. The discs are divided into segments and covered with a suitable filter medium and are connected through an appropriate valve assembly to a vacuum system, causing the proper segments to be under suction at the right time. It consists of a predetermined number of discs rotating in a tank, on a common shaft. The segments are of wood, grooved on a diagonal, for immediate and total drainage.ĭisc Filter is an alternate to the Rotary Drum Filter and has the advantage of being able to filter two or more products simultaneously with one unit. The filter proper is rotated by means of a totally enclosed worm gear drive which may be driven by belt, “V” belt, or direct connected motor through a speed reducer.Ĭast iron hubs are keyed to the central shaft, one for each disc, and respective segments are attached to these hubs with an effective drainage connection fastened with suitable, quickly removable clamps. The tank has dividers welded to it, for cake discharge, and can be completely divided into two or more compartments, to handle separate pulps, as conditions dictate. The Disc Filter is of rugged construction with each segment so made that it can be removed separately from others constituting the disc.Ī heavy duty central shaft, running in totally enclosed bearings, carries the predetermined number of discs, the whole being mounted on a welded steel tank, which, in turn, is supported on a heavy steel frame. In the metallurgical field the American filter finds its principal use today in dewatering of flotation concentrates. The cake will be so loose that it can either drop off or be scraped or rolled off easily. This is done by cutting off the vacuum and introducing a small quantity of 2 to 3 oz.
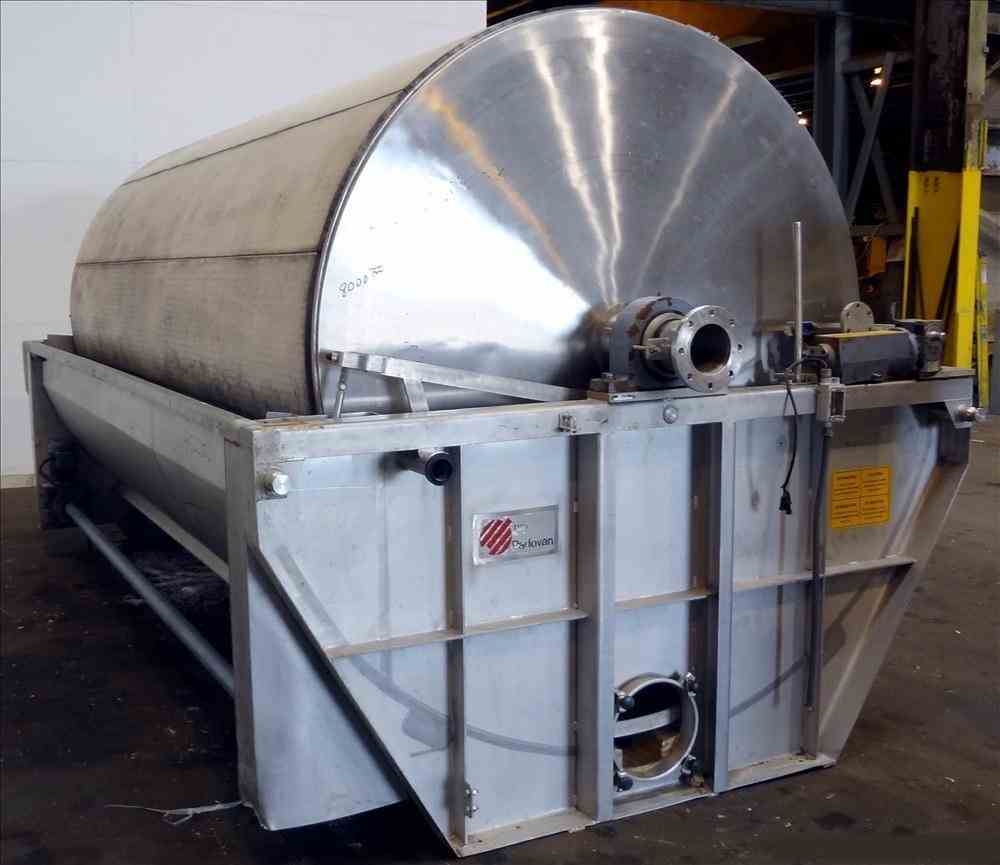
Now as dry as it can be made, the cake is in proper condition for discharging. After a sector passes out of the spray zone, vacuum still applied, a large portion of the wash that has replaced the original liquid is also drawn out. Fine sprays of solution or water then are applied to the cake, thereby displacing the original liquid left in the pores of the cake. As the disk slowly revolves, each sector in sequence rises from the pulp with vacuum still applied. In operation the thickness of the cake ranges from 1/8 to ¾ in., depending on the material being filtered. This filter is made by the Oliver United Filters in four sizes: 4, 6, 8½, and 12½ ft. The changing of filter cloths and the sectors is done easily and quickly. Inflation of the filter bags during each discharge period keeps the cloth in good condition, and the cake discharged has low moisture content. It occupies small floor space and presents a larger filter area or surface in proportion to space filled than any other filter. The American disk filter is a continuous machine of mechanical simplicity. The assembled disk and shaft section is shown in Fig. Wash water may be applied from spray nozzles. The disks are divided into independent and removable sectors. The lower halves of the disks are submerged in the slime tank. Disk Filters consists of a number of parallel, individual, cloth-covered disks mounted on a hollow shaft through which suction and compressed air may be applied.
